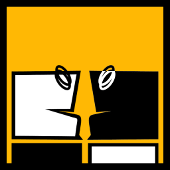



сегодня 10930 Подписчиков
Парадокс при производстве жалюзи
Обсуждения-аналоги
-
+36 / 2014-09-17 15:44:50,
[не прочитана]
Авторы
- Grey73 » Всем
- Павел Друбич » Grey73
- Grey73 » Павел Друбич
- SWS » Grey73
- Grey73 » SWS
- Сергей В. Сычёв » Grey73
- Павел Друбич » Grey73
- Grey73 » Всем
- Редакция » Grey73
- Grey73 » Сергей В. Сычёв
- Сергей В. Сычёв » Grey73
- Grey73 » Сергей В. Сычёв
- Сергей В. Сычёв » Grey73
- Grey73 » Всем
- Grey73 » Всем
- Сергей В. Сычёв » Grey73
- Grey73 » Сергей В. Сычёв
- Сергей В. Сычёв » Grey73
- Grey73 » Сергей В. Сычёв
- Grey73 » Сергей В. Сычёв
- Сергей В. Сычёв » Grey73
- Grey73 » Сергей В. Сычёв
- Сергей В. Сычёв » Grey73
- Grey73 » Сергей В. Сычёв
- Анна Каправчук » Grey73
- Сергей В. Сычёв » Grey73
- Grey73 » Анна Каправчук
- Grey73 » Сергей В. Сычёв
- Grey73 » Сергей В. Сычёв
- Сергей В. Сычёв » Grey73
- Grey73 » Сергей В. Сычёв
- Сергей В. Сычёв » Grey73
- Grey73 » Сергей В. Сычёв
- Редакция » Всем
- Виктор » Сергей В. Сычёв
- Сергей В. Сычёв » Виктор
Добрый день!
Одно из направлений нашей компании: собственное производство и реализация солнцезащитных систем по размерам заказчика.
На данный момент, причём в очередной раз, сложилась следующая ситуация:
При летнем ажиотаже производство не справлялось, поэтому было закуплено более производительное оборудование, но и это не привело к значительному росту объёмов выпускаемой продукции и сокращению сроков изготовления. Соответственно многие наши клиенты ушли, что привело сейчас к недозагруженности производства, потере выручки
Получается усиленно привлекали клиентов ценами, условиями, рекламой, при этом важно, вложились в модернизацию оборудования, увеличили количество работников, но к желаемому результату не пришли.
Мне поручено наладить полный цикл в этом направлении, но не знаю с какой стороны подступиться к проблеме. Прошу помочь.
С уважением,
Сергей.
Здравствуйте,
уточните:
- при новом оборудовании производительность осталась прежней?
- новое оборудование более производительно?
- потери времени при изготовлении возникают на операциях не связанных с новым оборудованием?
C пожеланиями,
Добрый день!
1)Увеличение производительности безусловно произошло, но совсем не такое как ожидалось.
2)Да, намного более производительно.
Немного информации для понимания:
основной время-затратной операцией по изготовлению горизонтальных жалюзи была нарезка-рубка ленты на ламели по размерам и продевание этих ламелей в лесенку.
Работник, исходя из размеров должен был:
-просчитать количество ламелей;
-вывести вручную на станке размеры;
-выставить также вручную пресса для пробивание отверстий;
-произвести пробный запуск, "нарубить" одну-две-три ламели;
-проверить соответствие размеров, ввести необходимые корректировки;
-запустить станок, вручную считая количество.
Затем передаёт готовые ламели другому работнику, который вручную каждую вставляет в лесенку. Для понимания трудоёмкости процеса: ламели идут через каждые два см, т.е. на 1м высоты изделий таких ламелей нужно продеть 50шт, причём через две-три-четыре лесенки, в зависимости от ширины изделия. Дальнейшие операции для окончательного изготовления изделия намного менее трудо- и время-затратны (хотя думаю здесь тоже может быть слабое место)
Сейчас стоит автоматический станок, в который нужно ввести только размеры изделия и на выходе мы получаем готовое нужное количество ламелей, вдетых в лесенки
3)На этот вопрос трудно ответить, так как до настоящего момента для меня цех был как "закрытая коробочка": заказы на входе, готовые изделия на выходе. Я курировал это направление только по финансовым отчётам
Чтобы разобраться в проблеме я понимаю, что нужно пройти по всей цепочке, но мне, привыкшему оперировать только цифрами в рублях и никак не связанным с производством человеком, нужна помощь.
Здравствуйте,
Один резерв виден сразу - уберите у рабочего операцию расчета ламелей - пусть этим занимается другой человек, т.е. экономим время на непосредственную работу оборудования.
правда, я так и не понял, почему же автоматический станок, который сам делает половину операций не обеспечил роста производства...
Ну и еще, я бы поработал со статистикой размеров изделий на выходе - наверняка есть повторяющиеся (окна ведь особым разнообразием не отличаются) - т.е. может существовать возможность наработки продуции на склад в несезон
Здравствуйте,
Один резерв виден сразу - уберите у рабочего операцию расчета ламелей - пусть этим занимается другой человек, т.е. экономим время на непосредственную работу оборудования.
Я написал, что на новом станке этого делать не надо, вводятся только размеры и никаких расчётов
правда, я так и не понял, почему же автоматический станок, который сам делает половину операций не обеспечил роста производства...
Вот я тоже не понял
Ну и еще, я бы поработал со статистикой размеров изделий на выходе - наверняка есть повторяющиеся (окна ведь особым разнообразием не отличаются) - т.е. может существовать возможность наработки продуции на склад в несезон
Этим вопросом можно заняться, но это не есть выход из ситуации. Начали появляться у меня мысли по проблеме, но пока не до конца. Н-р, если человек делал энное количество изделий за день (сейчас речь идёт о работе не на станке, а о других операциях), получал за это определённые деньги, которых ему хватает, то трудно его заставить увеличить производительность.
Уважаемый Сергей!
Отправил Вам по почте xls-файл с упрощенной формой техкарты ("лист трудоемкости" и "лист материалоемкости").
Попробуйте заполнить пока только 1 (для Вашего случая) - "лист трудоемкости".
Пока заполните там только поля:
- Операции
- Норма времени
- Число операций (план)
Прочее потом...
Спасибо,
Здравствуйте,
3)На этот вопрос трудно ответить, так как до настоящего момента для меня цех был как "закрытая коробочка": заказы на входе, готовые изделия на выходе.
1. Да, пройдите по цепочке.
2. Станок работает всю смену (загружен всю смену)?
3. Сколько времени теряется при переходе с заказа на заказ?
4. Много ли времени приходится на операции "ДО станка" (то есть, не дожидается ли он своих ламелей из-за "узкого места ДО")?
5. Много ли времени приходится на операции "ПОСЛЕ станка" (то есть, не скапливаются ли изделия из-за "узкого места ПОСЛЕ")?
С пожеланиями,
Спасибо! Начало следующей недели проведу непосредственно на производстве. О результатах обязательно отпишусь.
Уважаемый Сергей!
Начало следующей недели проведу непосредственно на производстве. О результатах обязательно отпишусь.
Да, пожалуйста, обязательно отпишИтесь.
Спасибо,
Добрый вечер.
Пару вопросов по заполнению тех-карты:
1)С основными операциями более-менее понятно, но насколько мелко надо раздробить эти операции? До вкручивание винтика?
2)Я правильно понял, что надо замерить эти операции отдельно, хотя они происходят параллельно?
Заранее спасибо.
С уважением,
Сергей
Уважаемый Сергей!
1)С основными операциями более-менее понятно, но насколько мелко надо раздробить эти операции? До вкручивание винтика?
Да.
2)Я правильно понял, что надо замерить эти операции отдельно, хотя они происходят параллельно?
Да. На первом этапе надо собрать продолжительность каждой операции и общие затраты времени (пока не общую продолжительность процесса).
Общую продолжительность процесса надо будет определить позже; надо будет построить диаграмму Гантта; тогда же будет учтена и параллельность операций.
------
Я предполагаю, что на Вашем предприятии есть технолог - он обязан Вам помогать в этой работе.
Спасибо,
Добрый день!
Нет у нас на производстве не технолога, не зав. производства, одним словом, "Анархия - мать порядка!". Единственный прямой руководитель - менеджер, но он должен заниматься продажами, а фактически львиную долю рабочего времени тратит на производство. Моя цель, как зам. директора, полностью выстроить, систематизировать процесс не только производства, но и всего отдела-направления, чем и занимаюсь.
С уважением,
Сергей.
Уважаемый Сергей!
а) Заодно поглядите разделены ли должным образом:
- "склад материалов, поступающих на производcтво",
- "само производство",
- "склад готовой продукции" ?
И каким образом оформляются приходы и внутренние перемещения материалов.
б) Если увеличения производительности не произошло на расчетную величину, то тогда где скопились материалы и как это оформлено?
То есть,
- от производства не поступило должного (увеличенного) числа заявок на склад 1?
- если нет, то почему?
- поступило увеличенное число заявок, но склад готовой продукции не оприходовал расчетного количества изделий?
- Тогда ГДЕ скопились "полуфабрикаты"? На каких операциях? Найдите сразу эти "операции".
- Если не найдете, то Вы должны начать подозревать кражи или "боковик" (собственное производство на базе чужого) или дать этому явлению иное объяснение; в любом случае - это глюк.
Если подобного разделения и внутренних накладных нет, то прямо сегодня введите это (см. п.а). Недопустимо, чтобы такого или более глубокого разделения не было, а все приходовалось "на производство" и там "варилось в общем котле".
в) Проверьте нормы расхода материалов. Посмотрите второй лист в файле отправленном Вам. Примите его во внимание (тоже надо будет заполнить).
Успеха,
Доброго времени суток!
Прошу прощения, что долго ничего не писал. Сразу скажу, что до производства я ещё так и не добрался, а занялся в первую очередь стадиями до и после него, а также решениями общих управленческих задач. Без этого, по моему мнению, бессмысленно лезть непосредственно в само производство. Попробую перечислить вкратце процессы, которые пытаюсь систематизировать, оптимизировать и стандартизировать (буду рад выслушать ваше мнение как правильно это делать):
1. Учёт рабочего времени сотрудников, в том числе в местных командировках. Заведены журнал учёта рабочего времени всего отдела и отдельно путевой журнал при выездах. Разработаны и доведены до каждого сотрудника соответствующие инструкции-регламенты.
2. Приём и обработка заявок клиентов. Разработаны инструкция, единый бланк заказа. Производится ежедневный подсчёт количества.
3. Контроль необходимых запасов комплектации на складе для беспрерывного производства. Разрабатываются нормы минимальных остатков.
4. Передача нарядов на изготовление в производство. Понятие наряда вообще отсутствовало, заявки диктовались на производство по телефону.
Три пункта требуют серьёзных изменений 1С или закупки специализированной программы под производство и продажи жалюзи. Думаем над этим совместно с программистами.
5. Время исполнение нарядов. Отслеживаю количества нарядов на входе и готовых изделий на выходе.
6. Передача готовой продукции. Разработана и внедряется инструкция.
Буду рад выслушать ваше мнение и вопросы по всем пунктам.
С уважением,
Сергей.
Доброго времени суток!
Как уже написал выше, замерами времени операций не занимался по причине отсутствия системы вообще как таковой. Обстановку можно обрисовать как "шараш-монтаж". Каждое новое введение воспринимается "в штыки" и пробуксовывает. Например, пытаюсь разработать и ввести внутренний унифицированный документ - единый бланк "Заказа", в котором:
-во-первых, собрана вся необходимая техническая информация (вид, размеры, управление, кол-во штук и т.д.);
-во-вторых, информация позволяющая отследить движение заказа во времени начиная от приёмки заявки, сдачи в производство и заканчивая упаковкой и отпуском продукции
-в-третьих, данные ответственных лиц на каждом этапе, в том числе покупателя при приёмке
-в-четвёртых, есть возможность вносить изменения, например, чтобы разбить процессы на этапы.
Сейчас все заказы принимаются по телефону, факсу, электронной почте, записываются в тетрадь, диктуются по телефону в цех, ещё несколько раз переписываются работниками, как-то там изготавливаются, иногда быстро, иногда не очень, т.к. есть много к этому причин: неожиданный завал заказами, так же неожиданная нехватка комплектации, отсутствие людей: ну заболел человек и пошёл в больницу или задержался в пробке. Клиенты периодически звонят по готовности заказов, когда приезжают им всё отгружается и оформляется по кв.м., менеджер лихорадочно ищет заказы в своей тетради, чтобы определить сколько же там штук в этой упаковке, вручную в Екселе составляет спецификации и ещё много чего вынужден делать.
И вроде бы мой документ максимально всё упрощает: менеджер "набивает" заявку в форму "заказ", распечатывает, передаёт в производство, отмечая время сдачи, после готовности один экземпляр крепится к упаковке, другой передаётся менеджеру с отметкой времени, осуществляет по нему отгрузку и всё.
Может я что-то делаю не так и действительно данное нововведение зло?
Прошу дать совет.
Уважаемый Сергей!
Вы все делаете правильно. Продолжайте.
Было бы странно, если бы никто не сопротивлялся :)
Спасибо,
Доброго времени суток!
Медленно, но уверено подбираюсь к производству. До него и после него пусть с "боями", но упорядочил процессы, т.е. теперь каждый заказ, каждое изделие сопровождается документом с отсечками времени на каждом этапе.
В одном из сообщений Вы писали о разделении склада комплектации, производства и готовой продукции. У нас этого разделения нет ни физического, ни документального, всё варится в одном котле. Проблема как в отсутствии помещений для этого, так и в людях.
Даже руководитель относится к этому скептически: "Брать дополнительно человека, чтобы считал эти "финтиклюшки" мы не можем себе позволить. Это выйдет нам дороже, чем потери, выявляющиеся при инвентаризациях."
Следует отметить, что в большинстве своём комплектация для жалюзи состоит из мелких деталей, т.е. комплектовать-выдавать со склада каждый заказ, даже пусть несколько заказов, действительно нерационально. А если ещё выписывать внутренние расходные накладные, то мы только и будем этим заниматься. Можно пойти по пути выдачи конкретного количества, н-р, кратно упаковкам, но куда девать остальное? - отдельного помещения для этого нет.
С одной стороны, проведённая мной даже выборочная инвентаризация показывает большие расхождения как в плюс, так и в минус, т.к. комплектация списывается по нормам, плюс за неё никто не отвечает. С другой стороны, эти расхождения выраженные в деньгах, которые и считает руководитель, не такие страшные.
Как можно решить данную ситуацию?
Уважаемый Сергей!
В одном из сообщений Вы писали о разделении...
Вот ссылка на это сообщение. Обратите внимание не только на пункт "а", но и на пункт "б".
Мы (с Ваших слов) имеем ситуацию, когда при использовании существенно более производительного оборудования, производительность участка не растет. И - при этом - число заказов было большим.
Мне непонятно:
Вариант 1. Если новая машина не работала (при большом числе заказов), то почему? Не было заявок на материалы, необходимые для производства заказов? Интересно почему? Вы уверены, что машина не использовалась налево при том, что, цитирую, "анархия - мать порядка". Почему Вы уверены в этом?
Вариант 2. Материала поступило на участок (в работу) "сколько-надо", а продукции произведено меньше.
Где тогда скопились необработанные материалы? Пойдите в цех и найдите эти скопления (либо самих материалов, либо полуфабрикатов). А если не найдете, то (при условии, что изложенное выше верно) уже не стоит писать слово "финтифлюшки" и "маленькие расхождения" и т.п.
--------------------------------------------------------------------------------------
Вдобавок Вы не учитываете, что отсутствие порядка на производстве - это не только расхождения в материалах и мелких деталях.
- Приплюсуйте упущенную выгоду от потерь Клиентов - то есть, несделанные продажи
- Приплюсуйте пустые затраты на скидки (т.к. привлекали низкими ценами и спец.условиями)
- Приплюсуйте обнулившийся эффект рекламы(и соответствующие затраты)
- Приплюсуйте увеличение числа людей
- Приплюсуйте дополнительную амортизацию оборудования, с которого нет "выхода"
- Приплюсуйте общий нерациональный ФОТ, когда большая часть зарплаты платится за "размазанный" простой, а не за работу
Эта все цена "финтифлюшек". Слежение за потоками материалов на производстве требуется не только для того, о чем многие думают (хотя и для этого), но и для понимания того, что происходит с производительностью. И для устранения общей дезорганизованности, потери от которой очень велики, но почему-то их никто не считает. А Вы посчитайте. Узнаете реальную себестоимость Вашей продукции. Многие, сделав это, узнают, что они давно торгуют в убыток, хотя имеют прибыль на бумаге.
--------------------------------------------------------------------------------------
Дополнительно:
- Думаю, что у Вас таки хватает площади. Поскольку
- весь материал у Вас уже физически размещен на той самой площади,
- а при беспорядке, обычно, место не используется более экономно и рационально, чем когда порядок наведен;
- более того, предполагаю, что и ощущение нехватки площадей возникает от того, что все в куче.
- Думаю, что у Вас избыточное число людей - так что, если проведете нормирование и наведете порядок, то дешевый кладовщик не будет той проблемой, которая должна Вас заботить.
- Это не так, что при введении внутренних накладных Вы "только и будете этим заниматься".Делается это следующим образом:
- В отделе продаж заказы от Клиентов заводятся в базу данных (например, "Жалюзи артикула N, синего цвета, кол-во и т.д.");
- Т.к., заранее известно, сколько и каких требуется материалов для производства каждого вида изделия, то в базе заранее сделана реализация, чтобы при заведении заказа автоматически "собиралась" внутренняя накладная, содержащая в себе все что требуется в нужном количестве для производства заказа (близкую задачу с учетом 1С подробно разбирали здесь);
- Все эти накладные видны на складе, и на складе все это заранее подготавливается к производству с указанием номера заказа и накладные распечатываются (при этом, время на печать одной накладной занимает, в среднем, не более 0,25 минуты);
- В начале смены начальник производства принимает на себя (расписывается в накладных) все материалы по заказам. Эти накладные состоят из нескольких частей и имеют индоссамент - то есть, несколько строк для передаточных подписей - так что, начальник производства, сдавая готовую продукцию на склад готовой продукции, использует то, что у него на руках (новых документов не создает);
- Сдавая смену, он должен "закрыть" все заказы выполненные за смену - то есть, в итоге, после ОТК, сдать по накладным на склад готовой продукции.
- Если по п.5. сдано меньше, то это значит, что а) производительность ниже нормативной (пусть объяснится) и б)нужное число материалов уже находится внутри цеха под ответственностью начальника производства, и он поэтому не может на те же заказы взять еще материал.
- Прозрачность картины позволяет решать множество самых разных задач, например, контролировать ритмичность производства, планировать его. И - при этом - никаких "финтифлюшек" и "только этим и будем заниматься."
В общем, храните порядок и он сохранит Вас.
Большое Спасибо,
Добрый день!
Спасибо за развёрнутый ответ.
Мне непонятно:
Вариант 1. Если новая машина не работала (при большом числе заказов), то почему? Не было заявок на материалы, необходимые для производства заказов? Интересно почему? Вы уверены, что машина не использовалась налево при том, что, цитирую, "анархия - мать порядка". Почему Вы уверены в этом?
Левые заказы были, но в них были замешаны дизайнеры-замерщики, менеджеры, сливавшие заказы нашим же дилерам, получая за это %. То есть в нашем случае, исходя из соотношения риск/выгода гораздо менее проблематично идти по этому пути, т.к. обнаружить такой слив сложно. Н-р, в последний раз замерщик и менеджер просто не поделили деньги и один настучал на другого. Очередные работники уволены - новые набраны, но я знаю, что ситуация периодически снова будет возникать.
Как этого избежать?
Вариант 2. Материала поступило на участок (в работу) "сколько-надо", а продукции произведено меньше.
Учёт минимальных остатков ведётся. Скопление полуфабрикатов отсутствует. Производство настроено только на исполнение заказов по времени (сутки), т.е. поступил заказ на производство - все бросились его делать и т.д.. Затор происходит при единовременном поступлении нескольких заказов или большого заказа, когда отодвигаются другие. Н-р, сейчас в ноябре мало заказов, но в декабре ожидаемый пик и мы "опять наступим на те же грабли".
Вдобавок Вы не учитываете, что отсутствие порядка на производстве - это не только расхождения в материалах и мелких деталях.
- Приплюсуйте упущенную выгоду от потерь Клиентов - то есть, несделанные продажи
- Приплюсуйте пустые затраты на скидки (т.к. привлекали низкими ценами и спец.условиями)
- Приплюсуйте обнулившийся эффект рекламы(и соответствующие затраты)
- Приплюсуйте увеличение числа людей
- Приплюсуйте дополнительную амортизацию оборудования, с которого нет "выхода"
- Приплюсуйте общий нерациональный ФОТ, когда большая часть зарплаты платится за "размазанный" простой, а не за работу
Эта все цена "финтифлюшек". Слежение за потоками материалов на производстве требуется не только для того, о чем многие думают (хотя и для этого), но и для понимания того, что происходит с производительностью. И для устранения общей дезорганизованности, потери от которой очень велики, но почему-то их никто не считает. А Вы посчитайте. Узнаете реальную себестоимость Вашей продукции. Многие, сделав это, узнают, что они давно торгуют в убыток, хотя имеют прибыль на бумаге.
Полностью согласен. Я всё это понимаю, но моя задача доказать и показать это руководству. Фактически приходится менять систему полностью. С вашими советами - это сделать гораздо легче.
Касаемо реализации:
1) 1С уже изменена под наши реалии: заявка от клиента вбивается и автоматически формируется и списывается количество необходимых комплектующих по норме. Как уже было сказано в одном из постов выше, для этого сделан универсальный документ заказ.
2)Склад комплектации хочу отделить от производства следующим образом: склад включает не начатые коробки, упаковки, рулоны, т.е. всё, что поддаётся лёгкому подсчёту. В производство передаётся по накладным всё пачками, исходя из потребности по факту.
Ещё раз, спасибо за ответы. Буду рад рекомендациям.
С уважением,
Сергей.
Добрый день!
Все ваши советы применены:
-Изготовление каждого изделия разбито на операции, подоперации. Таблица заполняется пока в ручном варианте, чуть позже обязательно сброшу Вам в электронном виде.
-Проводится постепенная инвентаризация комплектации, отделение склада, отпуск комплектации на производство по накладным.
-Налажен полный цикл документооборота.
Выявились следующие проблемы:
1)Все работники на производстве узкоспециализированы. То есть они могут выполнять работу и на других этапах производства, но с гораздо низким КПД. Поэтому при выпадении хотя бы одного работника из цикла производства (отпуск, отгул, больничный) мы не справляемся с объёмами. В зависимости от того какой специалист отсутствует, на этом участке и происходит "затор". Как раз наиболее заметно это было в пик сезона, летом - в период отпусков. Наём дополнительных работников не спасает ситуацию, так как только период обучения занимает минимум месяц, а для того, чтобы они достигли требуемой производительности нужно от 3-х месяцев.
2)Система заработной платы. Работники получают оклад плюс процент от объёма производства. И то и другое, то есть общая з/п зависит от отработанных часов. Минусы данной системы:
- больничные, отгулы, отпуска чувствительно влияют на з/п, т.к. часы минусуются и из оклада. Работник вынужденно выходит или с температурой или в выходные, в обоих случаях толку от этого мало.
- премиальный фонд фиксирован процентом. При увеличении объёмов нанимаются новые сотрудники и за счёт них старые получают премиальные столько же, т.к. фонд уже делится на большое количество работников. Получается у коллектива нет стимула напрягаться.
Помогите разобраться.
С уважением,
Сергей
Уважаемый Сергей!
До конца недели провожу семинары. В выходные или в начале след. недели отвечу.
Спасибо,
Спасибо, буду ждать, а пока своими силами.
Уважаемый Сергей!
Начну со второго пункта:
2)Система заработной платы. Работники получают оклад плюс процент от объёма производства. И то и другое, то есть общая з/п зависит от отработанных часов. Минусы данной системы:
- больничные, отгулы, отпуска чувствительно влияют на з/п, т.к. часы минусуются и из оклада. Работник вынужденно выходит или с температурой или в выходные, в обоих случаях толку от этого мало.
- премиальный фонд фиксирован процентом. При увеличении объёмов нанимаются новые сотрудники и за счёт них старые получают премиальные столько же, т.к. фонд уже делится на большое количество работников. Получается у коллектива нет стимула напрягаться.
Я не буду совершенствовать эту систему оплаты труда. Ее надо просто отменить. Сделайте это прямо в понедельник.
- Стоимость заказов не имеет отношения к тому, что делает рабочий в цехе;
- Сотрудник должен получать за ту работу, которую он выполняет;
- Размер заработной платы - при этом - определяется его (работника) стоимостью на рынке труда Вашего города и его личной результативностью, а не тем, на какое число участников делится "общак" на фирме;
- Производительность труда - при такой системе - падает до минимума;
- Поэтому, когда Вы пишете, что при приросте заказов не справляетесь с объемами, то это НЕ потому, что у Вас не хватает людей;
- Премировать надо за производительность, но производительность НЕ определяется количеством часов, которые сотрудник был в цехе; она определяется количеством заданий, выполненных им за нормативное время.
- Изготовление каждого изделия разбито на операции, подоперации. Таблица заполняется пока в ручном варианте, чуть позже обязательно сброшу Вам в электронном виде.
- И это поможет Вам разработать умные зарплаты для Ваших работников.
Про первый пункт:
1)Все работники на производстве узкоспециализированы. То есть они могут выполнять работу и на других этапах производства, но с гораздо низким КПД. Поэтому при выпадении хотя бы одного работника из цикла производства (отпуск, отгул, больничный) мы не справляемся с объёмами. В зависимости от того какой специалист отсутствует, на этом участке и происходит "затор". Как раз наиболее заметно это было в пик сезона, летом - в период отпусков. Наём дополнительных работников не спасает ситуацию, так как только период обучения занимает минимум месяц, а для того, чтобы они достигли требуемой производительности нужно от 3-х месяцев.
Во-первых, я думаю, что каждый Ваш опытный работник, находясь в цехе, не делает и половины нормативной выработки. Так что, когда Вы с этим разберетесь, то у Вас будет другая проблема: простои при полном комплекте квалифицированных специалистов. И Вы будете спрашивать: "Не распускать же их по домам" и т.п.
Во-вторых, приведите список тех квалифицированных операций (а не должностей), которым трудно быстро обучать.
Затем продолжим.
Спасибо,
Доброго времени суток!
В очередной раз огромное спасибо, что уделяете моим вопросам внимание. Бывают моменты, когда просто руки опускаются, так как приходится воевать со всем коллективом, в том числе и с директором-хозяином предприятия. Поэтому Ваши советы и поддержка так важны для меня.
Теперь по делу:
- Зарплата. Старую систему отменил, теперь срочно начинаю разрабатывать новую. В понедельник довёл информацию о введении новой системы оплаты в зависимости от производительности и выполненных работ, но ещё не был готов ответить на целый ряд вопросов, таких как конкретизация операций, соответственно стоимость этих операций, а также работ косвенно связанных с производством. Так что пока остановился на оплате за каждое готовое изделие с последующим разделением на отдельные виды работ. То есть у меня уже есть информация какие работы выполняются совместно, а какие конкретным работником. Теперь хочу проанализировать объёмы производства предыдущих периодов не в суммах, а в количествах изделий.
- Специализация. Начал составлять список, а он не составляется, т.к. действительно, операций, требующих высокой или вообще какой-либо квалификации практически нет. Разве что, за исключением работы на станке с ЧПУ для рубки ленты. А в остальном нужно просто набить руку. Здесь я, думаю, пошёл на поводу у отдельных работников, считающих себя незаменимыми.
Изучаю информацию на сайте по умным зарплатам.
"Добиваю" таблицу по операциям.
О всех новостях и возможных проблемах обязательно напишу.
С уважением,
Сергей.
- Зарплата. Старую систему отменил, теперь срочно начинаю разрабатывать новую.
Сергей!
Возможно, имело бы смысл в течение 2-3 месяцев выдавать зарплату "по-старому", но "табульку" давать со сравнительной таблицей - вот посчитанная "обычно", вот сколько сотрудник получил бы при новой системе зарплаты. Может быть, даже давать особо производительным возможность выбора между получением "старой" и "новой" зарплаты. Это снизило бы степень сопротивления персонала нововведениям и дало бы Вам работящих/активных/заинтересованных в переменах сторонников.
Уважаемый Сергей!
В очередной раз огромное спасибо, что уделяете моим вопросам внимание. Бывают моменты, когда просто руки опускаются, так как приходится воевать со всем коллективом, в том числе и с директором-хозяином предприятия. Поэтому Ваши советы и поддержка так важны для меня.
Вот пусть Вас дополнительно интервью с Фр. Тейлором вдохновит. Прочтите обязательно для "настройки мировоззрения" и понимания того, почему обязательно надо это сделать: "Добиваю" таблицу по операциям.
Поглядите также обсуждение про токаря (и корень, и обязательно все три ветки слева на панели).
Спасибо,
Добрый день!
Возможно, имело бы смысл в течение 2-3 месяцев выдавать зарплату "по-старому", но "табульку" давать со сравнительной таблицей - вот посчитанная "обычно", вот сколько сотрудник получил бы при новой системе зарплаты. Может быть, даже давать особо производительным возможность выбора между получением "старой" и "новой" зарплаты. Это снизило бы степень сопротивления персонала нововведениям и дало бы Вам работящих/активных/заинтересованных в переменах сторонников.
На моей практике постепенное внедрение равносильно закапыванию его в песок. Как правило сотрудники в таком случае успевают подстроиться, наложить старую систему на новую.
В моём случае понятно, что я не совсем готов полностью перейти на новую систему начисления зарплат, но уже в этом месяце каждый работник увидит, что получил премию не за часы, а за количество произведённых работ, изделий, то есть уже сейчас начнётся ломаться стереотип: "солдат спит - время идёт". Да, будет небольшая погрешность при начислении, но принцип будет соблюдён.
С наступающим Вас Новым Годом!
Решил написать, чтобы не создалось впечатление, что я всё бросил - это далеко не так.
Время после моего последнего письма потрачено совсем не впустую, но решить все проблемы "по мановению волшебной палочки" ну никак у меня не получается. Главное, продвигаюсь вперёд.
Проанализировал складские остатков, производство и сбыт за предыдущий и текущий года. На основе этого ввёл минимальные складские остатки по комплектующим, вывел эталонные показатели производства всех видов жалюзи в штуках и в квадратных метрах в месяц, неделю, смену. Соответственно премия в следующем году будет выплачиваться в зависимости от их выполнения.
К сожалению, не хватает ещё одного самого важного эталона - выполнение каждым работником N-го количества операций, т.к. не могу до сих пор заполнить предоставленную вами таблицу. Дело в том, что получается практически каждое новое изделие уникально по размерам. Получается нормы выполнения надо привязывать как то не только к видам изделий, но и к размерам. Например, чем больше вертикальные жалюзи по ширине, тем больше нужно сделать вертикальных ламелей, но сборка карниза занимает практически тоже время с небольшим увеличением. Чем больше высота горизонтальных жалюзи, тем больше ламелей надо нарубить. Кроме этого, есть множество модификаций даже этих основных двух видов.
Дайте пож-та эл. почту, чтобы я сбросил хотя бы что уже получилось, может Вы подскажите как быть дальше.
С уважением,
Сергей
Добрый день!
Заполнил таблицу самостоятельно, подсчитал нормы выполнения операций. Как и предполагалось, проблема не в производительности станка, а в дальнейших операциях по сборке изделий. Например, один квалифицированный работник выполняет операции:
-резка алюминиевой ленты на станке;
-резка верхнего нижнего карнизов на маятниковой пиле;
-пробивка отверстий под фурнитуру в карнизах на прессах
в среднем за 6 минут на одно изделии.
А вот сборка изделия длится в среднем 16 минут, в том числе 20% этого времени уходит на комплектацию изделия и упаковку - это у работника, специализирующегося на данном виде изделия. Привлеченный работник собирающий другие виды жалюзи, делает тоже самое значительно медленнее. Да и желания у него особого не чувствуется выполнять не свою работу. Ему легче затянуть время сборки своего вида жалюзи.
Теперь горизонтальные жалюзи собирают два человека, причём квалифицированный работник занят только непосредственно сборкой, а неквалифицированный подготовкой к сборке, упаковкой и, параллельно, обучается. Производительность стала в среднем 11 минут на изделие. В сезон планирую, что уже эти два работника будут заняты сборкой и третий \\"на подхвате\\". Таким образом производительность вырастет почти в три раза.
Остался открытым заданный выше вопрос по начислению премиальных данным работникам, а именно коэффициента, учитывающего суточное выполнение. В моём представлении формула выглядит следующим образом:
Премия = Оклад х Ршт х Ркв.м. х Рвр., где:
- Ршт. – рентабельность штук = (Штук в месяц/Эталон) х 100% ;
- Ркв.м. – рентабельность кв.м.= (Кв.м. в месяц /Эталонх) х 100% ;
- Рвр – рентабельность по времени. Показатель, учитывающий изготовление изделий за сутки. Как его правильно задать?
Дополнительный вопрос по бригаде замерщиков-установщиков. Как их заинтересовать в результате? Очень надеюсь, что ответите на вопросы.
С уважением, Сергей.
Уважаемый Сергей!
Дайте пож-та эл. почту, чтобы я сбросил хотя бы что уже получилось, может Вы подскажите как быть дальше.
Присылайте.
а) Мою почту видно в каждом моем сообщении этой темы.
б) Собственно, таблицу я Вам направлял по электронной почте. Посмотрите в поле "ОТ"
В моём представлении формула выглядит следующим образом:
Премия = Оклад х Ршт х Ркв.м. х Рвр., где:
- Ршт. – рентабельность штук = (Штук в месяц/Эталон) х 100% ;
- Ркв.м. – рентабельность кв.м.= (Кв.м. в месяц /Эталон) х 100% ;
- Рвр – рентабельность по времени. Показатель, учитывающий изготовление изделий за сутки. Как его правильно задать?
Слово "рентабельность" здесь лишнее - сбивает с толку. "Рентабельность" - это отношение прибыли к себестоимости. А у Вас речь идет о "Результативности".
Т.о., переведем:
- Ршт. = (Штук в месяц/Эталон) х 100% ;
- Ркв.м. = (Кв.м. в месяц /Эталон) х 100% ;
- Рвр = Результативность по времени. Показатель, учитывающий изготовление изделий за сутки. Как его правильно задать?
1. Непонятно зачем одно и то же выражать разными способами? Т.е., зачем нам выражать производительность и в штуках, и в квадратных метрах? В общем случае, необходимо и достаточно измерять именно "в штуках" - т.е., в натуральных единицах той продукции, которая выпускается. Могу предположить, что привычка измерять "в квадратных метрах" возникла из-за разнообразия типов изделий - так, что "штука штуке рознь" и не складывается, а квадратные метры можно посчитать в целом.
Могу также предположить, что Ваше перемножение результативностей по штукам на результативность по квадратным метрам связано с Вашим желанием разрешить следующую задачу: "Если стимулировать "за штуки", то будут любить простые и "короткие" изделия. А сложные и большие будут "динамить". Если же стимулировать за кв. метры, то - наоборот - "большие изделия" полюбят сильнее - т.к., на мелких больше времени уйдет на "переналадки" и "переходы" c заказа на заказ, чем на собственно выпуск квадратных метров".
Если перед Вами стояла такая задача, то решение в Вашем частном случае, Вы выбрали неверное. А если такой задачи не стояло и все издели относительно однородны по трудоемкости, то тем более нет причин использовать несколько разных единиц измерения одного и того же - считайте в "штуках".
2. Предлагаю Вам ввести "поурочную модель оплаты труда" и учитывать производительность ежесменно. Зная технологию, нормы времени на каждую операцию, а также видя те заказы, которые надо выполнить сегодня, можно задать эталон/урок на смену (то есть, вот эти заказы (Ваши работы), которые описаны в наряде помещаются по времени в сегодняшнюю смену - вот тех.карты = можете убедиться = это и есть "урок").
Всякому работнику, который свой "урок" в текущую смену выполнил, следует поставить Результативность = 100% за эту смену. Например, по техкарте Вы определили, что за конкретную смену могут быть выполнены 3 заказа 1 типа, 4 заказа 2-го типа и 7 заказов 3 типа. Значит выполнение такого задания = 100%. Не надо его перевыполнять, но и меньше делать тоже не надо. (Какая у работника возникает премия в случае выполнения задания, можем обсудить в следующем сообщении после того, как Вы ответите на этот пост).
Как видно, результативность по времени в этой модели тоже учтена.
3. Для единообразного учета выработки (в том случае, если изделия отличаются трудоемкостью), надо разделить изделия на группы и по определенным правилам (уже описаны) и каждой группе присвоить свой вес. Тогда можно будет посчитать какая вышла результативность, если вместо Вашего урока "3 заказа 1 типа, 4 заказа 2-го типа и 7 заказов 3 типа" они выполнили, например, лишь "2 заказа 1 типа, 3 заказа 2-го типа и 6 заказов 3 типа".
4. Про операцию умножения (в Вашем случае). Не забывайте, что перемножая значения меньше 1 (100%) Вы резко понижаете общее значение. Так, 80%*80%*80% в Вашей модели даст 50%, а не 80%. Равно и обратное: 120%*120%*120% даст 173%, а не 120%. (Поглядите материал из серии "Диалоги о зарплате" "Плюсы и минусы умножения").
Спасибо,
Добрый день!
Таблицу сбросил. В ней указаны усреднённые значения времени на каждую операцию, т.к. зависимость от величины изделия (размеров) существенная.
1) Согласен, что надо принять одну единицу измерения – штуки, но
-До меня учёт вёлся только в кв.м., у меня нет статистических данных по изготовлению изделий в штуках по предыдущим периодам. Только с этого года такой учёт стал вестись.
-выше я приводил показательные примеры зависимости трудоёмкости изготовления жалюзи от размеров. Учитывая изделия в кв.м. я хотел решить проблему веса.
2)заказы идут в режиме "нон-стоп", т.е. нет такого понятия, что с вечера или с утра разработал и выдал "урок" на смену. Бывает и «курим» целый день, а бывает аврал. У нас всё привязано к изготовлению любого заказа за сутки. Иначе клиенты уходят и им чихать на наш план. Существующая до этого года система оплаты, которую я ликвидировал, приводила к тому, что в 17.00 все работники бросали работу, чуть что - сразу больничный, летом - "строем" в отпуска. Жалюзи - сезонный товар и от этого никуда не деться. Основной заработок: март-июль. Конкуренция огромная. Сегодня надо сделать 100 штук, а завтра 0.
Таким образом, для меня главная задача заинтересовать работника работать тогда, когда мне нужно. Если он выполнит в рабочее время свою норму, но не сделает весь заказ, для меня проблема не решена.
3)Изделия разделены по группам по видам изделий, а также по трудоёмкости. То есть в таблице, например, к вертикальным жалюзи относятся все другие виды с аналогичными операциями и трудоёмкостью, к горизонтальным - также.
Так как известна производительность, намного легче планировать, но опять же повторюсь, планы часто меняются в течение дня.
4)Мне как раз нравится операция перемножения, так как виден резкий скачок при невыполнении/выполнении/перевыполнении плана-эталона.
Возможно помогут цифры за 2011 год.
Доля видов продукции в объёме производства:
Трудоёмкость 1 (горизонтальные) – 76,76%
Трудоёмкость 2 (вертикальные) – 23,24%
Уважаемый Сергей!
Я получил от Вас таблицу, спасибо.
Список ошибок, которые Вам надо исправить:
1. В поле "Операции" надо писать операции, а не их "пачку".
Например,
- "Сборка карниза (установка механизмов, суппорта, боковых крышек, резка и установка поворотной оси)" - так писать нельзя. Надо описать каждую операцию.
Нельзя также писать "установка механизмов" и т.д., поскольку за этой фразой скрывается набор действий.
2. В поле "Оборудование, инструмент" нельзя писать через запятую. Цитирую: "Пинцет, плоскогубцы, напильник" - так нельзя.
Не существует операций, которые один человек будет выполнять одновременно пинцетом, плоскогубцами и напильником. То есть, само перечисление инструмента через запятую говорит о том, что речь идет о нескольких разных операциях. Каждую из них напишите отдельно.
3. Удалена колонка "нормативное время", а оставлено только фактическое. Верните колонку и поставьте нормативное время. Если Вы его не знаете, сделайте пооперационный хронометраж и поставьте.
4. Удалена колонка "количество операций". Верните ее и после исправления ошибок 1-2 укажите соответствующие значения.
Обратите внимание. Вы пишете: "... чем больше вертикальные жалюзи по ширине, тем больше нужно сделать вертикальных ламелей,"
Если бы Вы не убрали колонку "количество операций", то Вы просто напротив каждой из операций, связанных с изготовлением вертикальных ламелей указывали бы разные их количества в зависимости от ситуации. Ни сами операции, ни их последовательность их от этого бы не менялись.
Аналогично, и с этим: "Чем больше высота горизонтальных жалюзи, тем больше ламелей надо нарубить" - никаких операций не добавляется, изменяется только количество. Это и надо указать.
5. Вы пишете: "... указаны усреднённые значения времени на каждую операцию, т.к. зависимость от величины изделия (размеров) существенная..." - это тоже одна из причин, почему надо писать каждую операцию и указывать количество операций. А "усредненное время" не надо указывать. Надо указывать точное.
6. нет такого понятия, что с вечера или с утра разработал и выдал "урок" на смену.
"Урок на смену" не разрабатывается с вечера или утра. Когда Вы хорошо заполните таблицу, которую я Вам прислал и не будете ее кромсать, то у Вас получится "урок навсегда". Поскольку "операционка", "последовательность", "распеределение между рабочими" и "нормы времени" будут установлены и не будут меняться. А когда придет конкретный заказ надо будет только указать соответствущие "количества операций". 2 минуты.
Не ленитесь. Вы хотите, чтобы Ваши рабочие не ленились, и Вы - не ленитесь.
7. Если он выполнит в рабочее время свою норму, но не сделает весь заказ, для меня проблема не решена.
Мне кажется, что эта фраза лишена смысла. А Вам?
8. Доля видов продукции в объёме производства: Трудоёмкость 1 (горизонтальные) – 76,76% Трудоёмкость 2 (вертикальные) – 23,24%
Трудоемкость измеряется в нормо-часах, а не в процентах.
===============
Я обратил внимание, что при производстве горизонтальных жалюзи у Вас двое одних и тех же рабочих выполняют операции и с ламелями, и с карнизами. Так лучше не делать = большие потери времени на переходы и т.п. При этом, потом подрезают ламели другие люди, которые затем переключаются на карнизы. Зачем? Суета и броуновское движение.
(Ну, в крайнем случае, можно еще было бы понять выполнение одними и теми же людьми резки карнизов и подрезания ламелей - чтоб от одного стола не отходить, так ведь у Вас эти работы делаются, как раз, разными людьми)
Подумайте, что мешает разделить между разными людьми: "работы с ламелями", "работы с карнизами" и "сборку". Общее правило: нельзя смешивать разнородные потоки работ в пространстве и у одних и тех же людей.
Успеха,
Добрый день!
В очередной раз, большое спасибо за подробный ответ. Таблицу начинаю заполнять по вашим рекомендациям со дня прочтения. Как будут конкретные результаты обязательно сообщу.
Уважаемые Коллеги!
Обязательно обратите внимание на материал "Скрытые простои и мнимые перевыполнения".
Спасибо,
Здравствуйте, Сергей Валерьевич!
Решаем схожую задачу на производстве. Можете ли выслать образец такой тех.карты?
Заранее благодарен,
С уважением, Виктор
Уважаемый Виктор!
450 долларов - и она Ваша. Можем выставить счёт в рублях по курсу на Ваш адрес или куда скажете.
Дайте знать, если ОК и тут же выставим.
Большое Спасибо,
На ту же тему
- Статьи по теме
- Обсуждения по теме
- Готовые решения по теме
Уровень зарплат на рынке и размер конкретного бизнеса не связаны друг с другом.
Есть определенные профессии, и есть их цена на рынке труда. Есть задания, которые поручены, и есть стоимость их выполнения. А также есть вопрос, который задают все: "Сколько платят такому специалисту в нашем городе?"
Конечно, хороший работник может и должен получать больше, а плохой — меньше. Однако, зарплата аналогичных работников в разных фирмах, в принципе, не может отличаться на порядки. Она может отличаться на 20–30%, но не в разы, тем более, не в десятки раз. Хотя выручка в крупном супермаркете и в "магазине на углу" может отличаться в сотни раз.
Мы сделали для рабочих больше, чем профсоюзы. Мы не только дали им зарплату большую, чем требовали профсоюзы на своих стачках, но и повысили выработку, сократив затраты труда и существенно снизив эксплуатацию. Рабочие в США с момента внедрения системы научного менеджмента перестали называться "пролетариями", они стали делать сбережения, покупать жилье и платить за хорошее обучение своих детей.
Таким образом, вопреки марксизму было показано, что повышение производительности (в том числе, скачкообразное) при капитализме не приводит к обнищанию рабочих. Наоборот, приводит к их обогащению".
Азбука консалтинга гласит: "Область постановки задач" (то есть, как они формулируются) достаточно часто не совпадает с "областью их действительного решения" (то есть, что случилось на самом деле). Например, желание "поднять командный дух", "сплотить коллектив", "ввести мотивацию от результатов всей компании" и т.п. – это нередко борьба со следствиями, а не с причинами.
Недавно наш знакомый консультант Mister Any получил следующий запрос: "Для подкрепления командного духа мне хочется ввести в отделе продаж доплату за выполнение плана всего отдела. Какой размер оптимален по отношению к общей зарплате сотрудника и к чему одна должна быть привязана? Рассчитываю на Вашу помощь". Подпись: Mr. Heart".
Недостаток 1 (из 9-ти).
Неучет того факта, что сумма сделки и трудоемкость выполнения работ не связаны между собой. Соответственно,
1.1. Крупный разовый (иногда нежданный) "оборотистый" заказ не влечет за собой дополнительной трудоемкости, а зарплату увеличивает и в результате расслабляет сотрудников.
И наоборот. Когда основная работа по обслуживанию долгожданного Клиента только начинается, а новых поступлений не предвидится, сотрудники "правомерно" интересуются: почему при больших стараниях и трудозатратах, чем в прошлый "прибыльный" месяц, их зарплата "падает".
1.2. У сотрудников невольно вырабатывается неприязнь к дешевым товарам и услугам, стремление избегать работы с ними и соответствующее отношение к Клиентам, которые их покупают. Так, в иных магазинах у стенда с кофеварками/кофемолками (условно) продавца можно и не дождаться (в отличие, например, от стенда с проекционными ТВ).
Как результат, премия "непрозрачна". Связь оплаты с результатами труда пропадает...
Производительность работника задаётся технологией. Эта мысль общеизвестна... В статье Авторы обращают внимание лишь на зарплатную часть проблемы...
Порой руководитель вводит новую систему оплаты труда, потому что его не устраивает "вялый" темп работы, низкая производительность сотрудников, "размазывание" небольшого объёма работы на весь день и проч. Но при установлении новых планов, заданий на смену допускается ряд управленческих ошибок, которые приводят к мнимым перевыполнениям при наличии скрытых простоев.
В связи с этим несколько полезных рекомендаций, как планировать производительность.
Если Вы бываете в Европе по делам бизнеса или с частными целями, найдите время заехать к нам в Прагу. На консультацию, на стажировку, на деловой завтрак. За свежими идеями, за новыми методиками, за иной обстановкой и за иными возможностями.
В Праге Вас встретят наши лучшие эксперты. Мы предложим Вам качественные программы бизнес-обучения по-европейски. В том числе, сделанные "под Вас". В том формате, в каком удобно Вам.
Идея проекта и руководство: С.В.Сычёв
Редактор: О.И. Дейнега. Web-Master: Р.А. Лушов.
Политика конфиденциальности